Interesting matter, even if what actually rules is the wallet .
The housing part of the camper, the cell , can be made in various ways and with various technologies, and the final products that are obtained are different from each other. But even if some cells are better than others, more insulating and less subject to specific problems, with a little organization and some intervention, all campers can be used , in normal situations, both in summer and in winter, both at the sea and in the mountains.
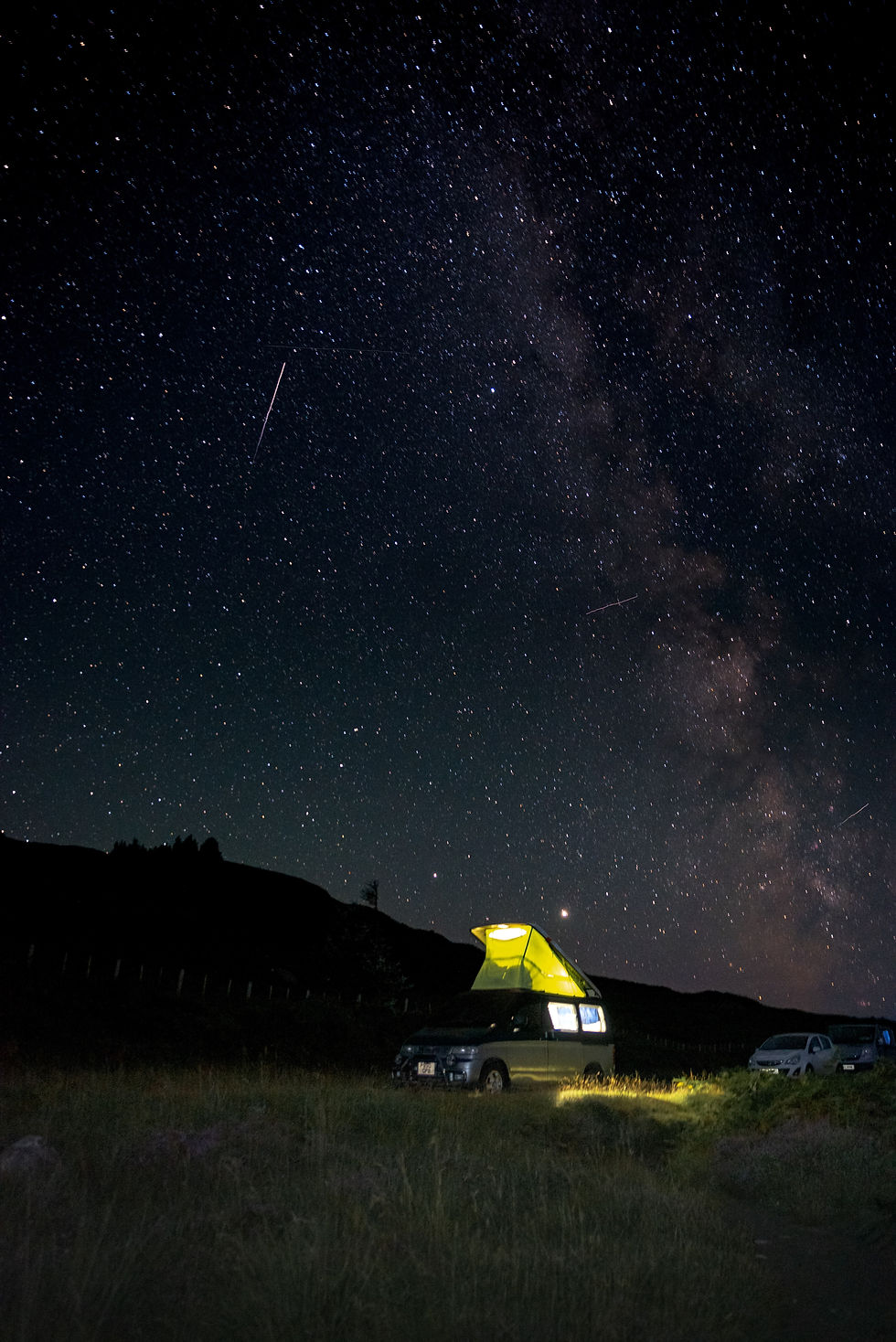
What does "normal situations" mean? A few degrees below zero do not scare anyone , furthermore, knowledge of one's vehicle, its limits and its characteristics counts . My advice is to do things step by step and never put yourself in potentially dangerous situations. Do you want some advice for winter use of the camper? Read here .
I had some snowfall in my camper life , I remember that from my first camper I was able to remove the snow from the roof easily, with a broom it slipped away immediately. In the second camper, on the other hand, it remained attached to the roof and I struggled a bit to remove it. Why? In the first case, the insulation wasn't "fantastic" , and the snow in contact with the roof (which lost some heat") softened and came off immediately, in the second case, the insulation was much better (one of the best on the market of those years), the heat did not reach the snow which, with the cold outside at night, froze and stuck together. But a few weekends in the mountains I did it with both the first and the second.
Let's go back to the cells, I would divide them into three groups: those in sheet metal , typical of pure vans/campers, those monobloc in fiberglass , made by some specialized manufacturers, those in sandwich panels , used in all industrially produced campers.
sheet metal . They have some undoubted pros: they are free from infiltrations, they are robust and have automotive characteristics, external maintenance and repairs can be done by any body shop. On the other hand, they are more difficult to insulate, they offer smaller internal spaces, the set-up is conditioned by the load-bearing structure and shape.
Fiberglass monoblock . The cell is made of fiberglass in a single block, has no joints and is therefore free from infiltrations (if intact). The insulation is perfect, as these cells are formed by two shells, one inside the other, between which the insulating layer has been inserted. They are designed ad hoc by the fitter, the interior spaces are optimized for fitting out and often feature interesting interior solutions. They cost.
Sandwich panels . The cell is formed by panels composed of an external covering, an internal frame, insulating material, an internal covering. Most motorhomes are built in this way, but what changes is the composition of the sandwich: externally it can be in aluminum ( Al ), or in fiberglass ( vtr , but do not confuse motorhomes in fiberglass panels with monobloc ones, they are completely different), Arca has its own external coating called AluFiber (aluminum + fibreglass, used for the walls); the internal frame can be made of wood (until a few years ago they were all like this), or insynthetic material , the latter to be preferred because it does not rot in case of infiltrations; the insulating layer can be EPS (expanded polystyrene), used by some manufacturers, XPS (extruded expanded polystyrene, more compact and insulating than EPS), used by many manufacturers, PU (expanded polyurethane), as far as I know, used only by Hymer, Styrofoam RTM (an evolution of extruded polyurethane foam), used, I understand, by Carthago, Niesmann+Bischoff, Concorde; internally the sandwich can be in fibreglass, aluminum or wood.
Just a few examples of the composition of the sandwich walls (roof and floor may be different) from current productions : Arca Alufiber/xps/vtr, Laika Al/xps/wood, Elnagh vtr/xps/vtr, PLA vtr/eps/vtr, Burstner fiberglass/xps/wood, Hymer fiberglass/pu/wood, Carthago Al/rtm/Al.